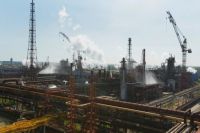
Понятно, что в каждой тонне продукции и в каждом заработанном рубле – вклад всего трудового коллектива предприятия, настоящих профессионалов своего дела. А возглавляет этот коллектив директор Филиала «Азот» Дмитрий Иванов, который сегодня рассказывает о том, что сделало возможным производственные успехи и о дальнейших планах лидеров химической промышленности Верхнекамья.
«АиФ-Прикамье»: - Дмитрий Владимирович, при объемах производства «Азота» рост даже на доли процента является весьма внушительным. За счет чего предприятие смогло увеличить выпуск продукции на десятки тысяч тонн?
Дмитрий Иванов: - С 2010 г. ОАО «ОХК «УРАЛХИМ» реализует проект технического перевооружения «Азота». Рост 2011 года – итоги мероприятий, реализованных в 2010 г. Капитальные ремонты тогда были проведены практически во всех технологических цехах – аммиака, карбамида, крепкой азотной кислоты, водоустойчивой аммиачной селитры, неконцентрированной азотной кислоты, гранулированной аммиачной селитры, нитрит-нитратных солей, высших алифатических аминов, переработки газов.
Перечислю только основные проекты. В цехе слабой азотной кислоты одновременное проведение ремонта агрегата унифицированной кислотной линии и остановочного капитального ремонта одного из отделений позволило увеличить выработку слабой азотной кислоты. В цехе карбамида модернизированы компрессор углекислого газа и колонна синтеза. Это позволило обеспечить стабильную работу основного оборудования цеха и увеличить выпуск карбамида на 100 тонн в сутки. А благодаря работам по модернизации колонны синтеза аммиака предприятие смогло увеличить выпуск этой продукции до 1700 тонн в сутки и снизить потребление природного газа. Этого удалось достигнуть за счет монтажа змеевика технологического газа в конвективной зоне печи риформинга. Промывка оборудования фурфуриловым спиртом позволила уменьшить коррозионное влияние смол и работать на более высоких нагрузках. Технический надзор за реализацией этого проекта вела фирма Ammonia Casale SA (Швейцария), один из мировых лидеров модернизации производств азотных удобрений. Все работы по применению новой технологии очистки курировал профессор, лауреат Нобелевской премии Иосиф Лейтес.
«АиФ-Прикамье»: - То есть, в 2012 году «Азот» вновь увеличит выпуск товарной продукции, ведь в 2011 году техперевооружение продолжалось?
Д.И.: - ОАО «ОХК «УРАЛХИМ» исповедует принцип постоянного улучшения. Действительно, мы завершили очередной этап капремонтов, в которых участвовал практически весь наш коллектив. В модернизацию оборудования предприятия в 2011 году вложено около 850 млн.руб.
В минувшем году основное внимание было обращено на модернизацию производства аммиака. В цехе крупнотоннажного агрегата аммиака (1А) проведены работы по реконструкции блока очистки конвертированного газа от углекислоты. Залитый в систему новый абсорбент – метилдиэтаноламин – позволит предприятию уже в этом году увеличить выпуск аммиака и снизить удельный расход пара. Кроме того, переход на новый абсорбент снизит коррозию аппаратуры и сократит удельный расход тепла на стадии очистки. В цехе также установлено новое оборудование – переливные тарелки и угольные фильтры для очистки раствора, промдисорбер, котлы-утилизаторы и подогреватель природного газа, заменена футеровка печи риформинга и проведена реконструкция паровой турбины.
В цехе слабой азотной кислоты на трех агрегатах отремонтированы газовые турбины, компрессоры, теплообменное оборудование, проведен капитальный ремонт водооборотных циклов. Пневматическая система управления агрегатами заменена на микропроцессорную – установлен программно-технический комплекс на базе системы Centum от японской фирмы Yokogawa. Новая система позволит повысить контроль над технологическим процессом производства кислоты и облегчит условия труда.
В цехах высших алифатических аминов и нитрит-нитратных солей выполненные мероприятия стабилизировали технологические режимы и продлили ресурс использования оборудования. В цехе нитрит-нитратных солей, в частности, заменена ловушка нитрозного газа на инверсионной установке – вместо аппарата из нержавеющей стали установлен титановый. Также в цехе выполнен ремонт бункера кальцинированной соды и коллектора оборотной воды, заменены два сборника маточного раствора, отремонтированы футеровка контактного аппарата и станция натяжения платиновой сетки.
Конечно, я надеюсь, что эти и другие мероприятия позволят нам продолжить устойчивый рост. В пользу этого свидетельствуют итоги работы уже первых недель 2012 года. В случае, если мы продолжим работать на таком же уровне, то общий объем производства за 2012 год превысит 2011 год, как минимум, на 3%.
«АиФ-Прикамье»: - А как предприятие справляется с отгрузкой возросших объемов продукции потребителям?
Д.И.: - Естественно, проект технического перевооружения предприятия учитывал этот важный фактор.
Уже к началу навигации, к маю прошлого года, мы завершили реконструкцию заводского причала. Здесь построен новый бункер под насыпь готовых удобрений, удлинен железнодорожный путь, на погрузочном конвейере заменены главный транспортер и редукторы. Благодаря внедрению нового оборудования, увеличилась скорость движения транспортной ленты, что позволило увеличить скорость загрузки судов. В итоге с собственного причала предприятие отправило 350 тысяч тонн продукции, увеличив тем самым отгрузку на 150 тысяч тонн, по сравнению с 2010 г.
И, наконец, уже в 2012 году, в начале января, мы смогли увеличить погрузку гранулированной аммиачной селитры в мягкие контейнеры (МКР). Для увеличения отгрузки удобрения в МКР выполнен комплекс взаимосвязанных мероприятий. Усовершенствованы точки погрузки, установлены новая лебедка и скоростные погрузочные устройства «Demag». А для обеспечения подачи большего числа вагонов под МКР реконструированы железнодорожные пути и приобретен новый тепловоз. Если ранее максимальный суточный объем отгрузки достигал 30 полувагонов или 1,8 тыс.т МКР, то теперь за сутки в 44 полувагона мы можем отгружать более 3 тыс. МКР.
Таким образом, мы не только увеличили объем отгрузки, но и повысили качество клиентского сервиса, выполняя все заявки потребителей по формам отгрузки продукции.
Кроме того, мы существенно повысили вариативность способа отгрузки продукции: теперь мы готовы без ограничений обеспечивать отгрузку нашего основного продукта – аммиачной селитры – тем видом транспорта, который выгоден нашему потребителю. А это, несомненно, дополнительно повышает конкурентоспособность продукции нашего завода.
«АиФ-Прикамье»: - Дмитрий Владимирович, как правило, увеличение объемов производства, особенно на химическом предприятии, ведет к увеличению вредного воздействия на окружающую среду. Как на «Азоте» решают эту проблему?
Д.И.: - Одной из стратегических целей компании «УРАЛХИМ» является достижение экологической безупречности производства. За три прошедших года поступательного движения к ней филиал «Азот» смог существенно снизить основные виды воздействия на окружающую среду: сбросы в воду, выбросы в воздух, образование отходов.
Может быть, для кого-то это прозвучит парадоксально, но улучшение экологической обстановки происходит одновременно с увеличением объемов производства и улучшением качества нашей продукции. Ведь раньше считалось: чем больше удобрений выпускаешь – тем больше загрязнений. Нам удалось изменить такой подход. Ведь на «Азоте» находит применение все новое, что дает технический прогресс. А современные технологии априори являются максимально экологически эффективными.
Таким образом, комплексная реконструкция и модернизация позволяет нам не только стать одним из мировых лидеров производства минудобрений, но и существенно снизить вредное воздействие на окружающую среду, улучшить условия труда людей. В частности, за 2011 г. снижение по сбросам загрязняющих веществ произошло по аммоний-иону (около 40%), взвешенным веществам около 12%), карбамиду (около 42%), натрию (около 26%), калию (около 11%). На 29% на предприятии повысился объем реализации и утилизации отходов. Кроме того, снижены выбросы загрязняющих веществ в атмосферу – по оксидам азота на 5,7%, а по аммиачной селитре на 25,8%.
«АиФ-Прикамье»: - Последний вопрос. Каковы планы дальнейшего развития предприятия?
Д.И.:- Мы сосредоточим усилия на совершенствовании работы предприятия, дальнейшем повышении качества продукции и модернизации производственной инфраструктуры, снижении воздействия на окружающую среду и доли ручного труда.
Основными проектами, которые нам предстоит реализовать, являются приобретение и монтаж классификаторов готового продукта в цехе карбамида для улучшения качества продукции, техперевооружение кратцер-кранов в цехе гранулированной аммиачной селитры для дальнейшего увеличения отгрузки, внедрение АСУ ТП в производстве концентрированной азотной кислоты и другие. Продолжим реконструкцию водооборотных циклов для снижения водопотребления и сброса сточных вод. Большой проект – ремонт бытовых помещений – раздевалок, душевых, санузлов во всех цехах.
Таким образом, постепенно на месте старого «Азота», который в 2012 году отметит 80-летие, постепенно возникнет новое современное предприятие. Огромный потенциал и хорошие перспективы Филиала «Азот» позволяют смотреть в будущее с оптимизмом. Я уверен, что мы сможем создать лучшее предприятие отрасли.